Silicone Coated or Silicone Impregnated Fabric?
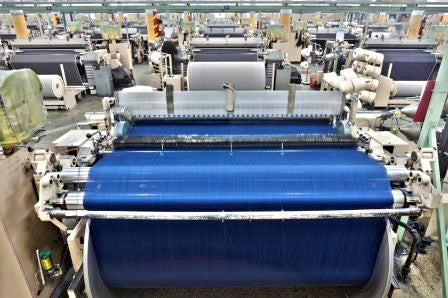
I frequently get asked if the “Sil-Nylon” fabric I use for LightHeart Gear is ‘silicone coated’ or ‘silicone impregnated’. There really is no difference between those terms. And don’t let any one tell you differently.
Some definitions to get us started -
Impregnated: soaked or saturated with a substance.
Coated: Having a coating; covered with an outer layer or film
But lets start with a bit of information about how fabric is made –
First, the fabric is woven. But it’s not that simple yet – lets talk about the thread used to weave it. Many fabrics are woven of “greige goods” This means “raw goods”, generally a white-ish color and the fabric after it is woven is ready to be dyed. Generally by means of “Vat dying” (sometimes referred to as stock dyed fabric) where long lengths of fabric are dyed a single color.
Then there is “Solution dyed fabric”. This is where the raw materials used to make the thread is already dyed a particular color. The pellets of nylon or polyester are colored and when melted and extruded through spinnerets, the thread is the final color of the fabric. This means that the color runs through the entire fiber, like the orange of a carrot, not just on top, like the red of an apple
Once you have the thread – greige goods or solution dyed, it is woven into fabric. The link below explains the warp (lengthwise threads of fabric) and weft (crosswise threads) being managed on a loom. In the video, they are making greige goods. This way, they can weave a large quantity of fabric, (10 to 20 thousand yards or more) cut it into smaller rolls and dye each roll a different color. If this was woven as solution dyed fabric, they would have to stop and re-warp the loom with a different color each time they needed to change colors – Warping a loom takes a lot of time.
Vat dying is fine for solid colors, but what about prints? Check out the videos below. The ‘repeat’ of the print – how long it is running up the length of the fabric depends on the circumference of the rollers. Each roller prints different motifs and colors onto the base ‘greige’ fabric.
Printing Fabric & Printing fabric
After fabric is printed or vat dyed, it can then be ‘finished’. Finishing can involve different coatings. This could be a ‘permanent press’ finish, or in the case of the fabrics used for LightHeart Gear, it involves a silicone coating. Now here’s where you get to decide if this is “coated” or “impregnated”. The video below is the only one I could find on line, it’s not great, but you get the idea. The greige goods, once washed, dyed, dried and then rolled is now fed through another machine, where the (silicone) coating is applied to the surface of the fabric. The recipes for the coatings are usually proprietary to the manufacturer, but the process is the same. The liquid coating is applied to the fabric just before the fabric goes between rollers and the coating essentially gets ‘squeegeed’ onto the fabric. The specific coating and thickness is what determines the waterproof rating. After the fabric goes through the squeegee, it then enters a long drying chamber that is heated to dry the fabric. When the fabric comes out the other end of the dryer it gets rolled back up. In the case of the fabrics we use at LightHeart Gear, they then go back though this process with a slightly different coating applied to the other side of the fabric.
So now, is this ‘impregnated’ or ‘coated’? How do you define impregnated? Remember how thin the fabric is to start with, when the silicone is applied to the fabric, the fibers will soak up the coating to some degree, and it will migrate through to the other side of the fabric (at least with the first pass of the coating). Either term, the fabric becomes WATERPROOF. There is no air permeability.
Coating fabric: This is not the best video, but it’s all I could find.
Because it is a slightly imperfect method of applying the coating to the fabric – some areas may have a little more, some a little less coating, the fabric is tested in a minimum of 6 different locations through out the length of the roll to determine the waterproof rating. (I’ll leave that for another blog post). That means some areas are higher and some may be a little lower. We have had our fabric independently tested by several third parties and it has consistently rated close to 4000 mm of water hydrostatic head.
The fabrics LightHeart Gear uses are all vat dyed (except for the camouflage fabric which is printed) and then coated on both sides with silicone, and in the case of the Royal Blue and Espresso Brown fabrics, one side is coated with silicone and the other with a polyurethane coating.